Expansion Joint
Providing comprehensive expansion joint services and expert advice.
We pride ourselves as expansion joint contractors on our ability to deliver on every aspect of your project, from the initial site survey through to the installation of expansion joint.
Our expertise ensures seamless integration of expansion joint systems, enhancing the durability and performance of your structures. Trust AWS Services to deliver precision and reliability, our solutions are tailored to meet your construction needs with excellence.
Our company operates in WA, QLD, NSW & VIC. Contact one of our team today to find out if we can assist your project!
Concrete Expansion Joint
A concrete expansion joint is a strategically designed gap that accommodates the natural expansion and contraction of concrete due to temperature fluctuations. By providing a break between the concrete and adjacent structures, these joints prevent stress accumulation, which can lead to unsightly and structurally compromising cracks.
Using AWS for your expansion joint needs ensures that your construction projects benefit from expert knowledge and high-quality materials, enhancing the durability and longevity of your structures. Our team is dedicated to providing tailored solutions that address your specific requirements, ultimately saving you time and money by preventing costly repairs down the line.
Bridge Expansion Joint
Bridge expansion joints are engineered to adjust their length and accommodate movement or deformation caused by shrinkage, loads, or temperature variations. These joints are crucial in maintaining a seamless and safe traffic flow between bridge structures and connecting segments.
Engaging AWS for your expansion joint needs ensures that you benefit from our expertise and commitment to quality. We provide solutions that enhance the durability and performance of your infrastructure.
Expansion Joint Repair
At AWS Services, we specialize in the repair and maintenance of expansion joints, providing comprehensive solutions to address damaged or deteriorating joints and cracks. Our services include the use of advanced Hypalon bandage systems, which are meticulously sealed and secured on all sides of the expansion joint or crack using high-performance epoxy resin adhesives.
Expansion Joint Waterproofing
Waterproofing materials used in expansion joints must be flexible to accommodate the joint’s movement without cracking. This flexibility is crucial to maintaining the integrity of the waterproofing and ensuring long-term durability.
Ensure your expansion joints endure with AWS Services’ expert waterproofing solutions. Our dedicated team will enhance your expansion joints resilience against weather and wear, ensuring lasting protection and peace of mind.
Expansion Joint Installation
Our expansion joint installation service is suited to meet your needs. Our team will use our knowledge and expertise to find the best solution to your project.
With operations in 4 states (Queensland, Western Australia, Victoria and New South Wales), We have the resources and people to conduct works of many different shapes and size. Our people can provide the best assistance and expert advice to ensure the customer is satisfied. contact us today to find out more!
Expansion Joint Projects
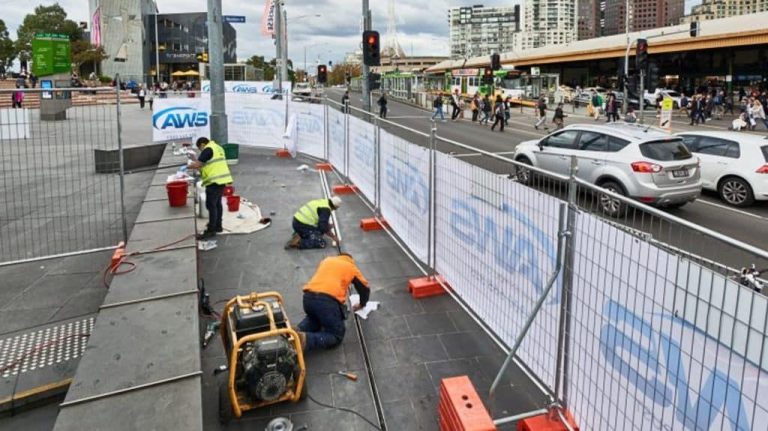
Federation Square
AWS was engaged to assess and remove faulty expansion joints at the iconic Federation Square in Melbourne. On determining the correct product and a fit for purpose solution, we installed a variety of expansion joints across the site to suit movement requirements of the site.
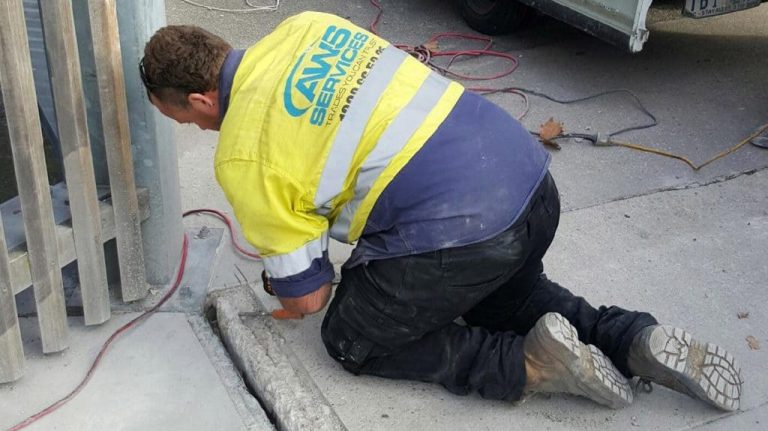
Sandbridge Bridge
AWS carried out the refurbishment of the expansion joints on both the Sandridge bridges. A granor system was used to allow for the constant movement in these structures. Temporary traffic management was used. The job was performed during normal working hours and was completed on time and on budget.
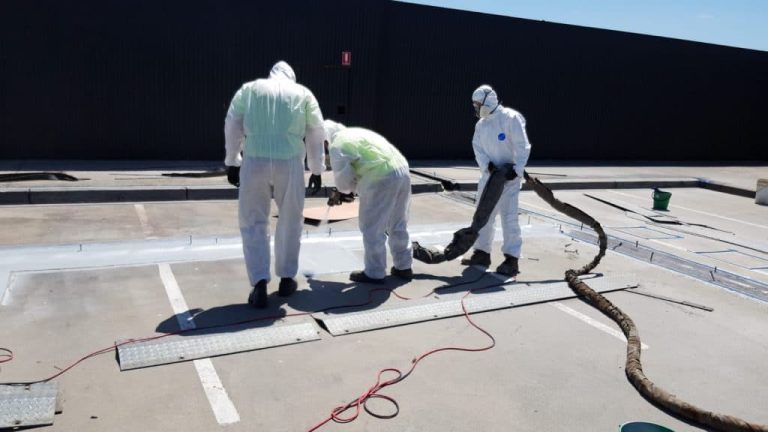
Westfield Carpark
AWS has created a system whereby the existing expansion joints were not removed, the combi joint was left in place and a high strength coating was sprayed over the existing combi joint giving it extra strength and waterproofing the expansion joints.
FAQs About Expansion Joint
In building construction, an expansion joint is considered a mid-structure separation made to relieve stress on building materials caused by building movement. Keep in mind that building movement at expansion joint is mainly included by:
- live load deflection
- static load deflection
- seismic events
- sway caused by wind
- thermal expansion and contraction caused by temperature changes
Since the joint bisects the whole structure, it marks a gap through every building assembly, such as walls, decks, foundation floors and walls, plazas, roods, planters, and more. That gap should be filled to restore the soundproofing, fireproofing, waterproofing, air barrier, trafficable surface, roof membrane, and other functions of the building elements it bisects.
Further, expansion joint systems are utilized to bridge the gap and reestablish building assembly functions while accommodating the anticipated movements.
Expansion joints are applied in concrete to avoid expansive cracks due to temperature change. Concrete experiences expansion because of high temperature when in a narrowed boundary, leading to cracks. Expansion joints are given in piping systems, railway tracks, sidewalks, bridges, buildings, pavements, slabs, ships, and other structures.
Concrete isn’t an elastic substance, and thus it doesn’t stretch or bend without failure. Nonetheless, concrete moves during shrinkage and expansion, due to which the structural elements shift a bit. To avoid the risky effects of concrete movement, numerous expansion joints are integrated into concrete construction, including paving slabs, foundations, walls, and roof expansion joints.
Such joints must be thoroughly designed, positioned, and installed. When a slab is placed evenly on surfaces exceeding the face, the expansion joint will be necessary to lessen stress. Concrete sealers may also be utilized for filling gaps made by cracks.
Expansion joints are made to absorb vibration, noise, and movement within a ducting or piping application. There are different types of expansion joints, including:
- Foam-type – These are two types: impregnated open-cell foam and closed-cell foam. The former is composed of a low-density, cross-lined ethyl vinyl acetate material, creating a strong rubber-like material that sits closely together but isn’t connected. The latter comprises pre-compressed impregnated foam hybrid material and silicone that needs a silicone surface sealant to seal the substrate voids.
- Compression seal – These are often classified as cellular or neoprene, designed to accommodate movements of less than 2 ½ inches, and don’t allow staged construction.
- Winged joint – These are made of thermoplastic materials and behave like a compression seal but have added “wings” integrated to offer secure attachment.
The most critical purpose of an expansion joint is to expand the surrounding cement. Expansion joints also offer the concrete somewhere to go as it moves. Pressure builds up and potentially cracks a weak spot in the slab without a gap for the concrete to expand into.
Concrete moves with changes in temperature, movement in the earth, and vibrations. Joints also help those concrete strong while the soil settles around it. You can see these expansion joints pretty much everywhere concrete is used on the ground. Further, gaps in the patios, walkways, sideways, and even roads use these expansion joints to avoid cracking.
Expansion joints in masonry walls are provided every 125 feet, and in concrete or steel structures or roofs, joints are positioned every 200 feet or so. They must be positioned at junctions of separate structures, elevator shafts, and stairwells.
Bridges made of concrete will expand and contract a bit for many different reasons. That includes ice, settlement, shrinkage of the concrete, temperature changes, and even the weight of vehicles. Bridge expansion joints permit the concrete to expand naturally and contract without even cracking.
The rubber expansion joints are positioned at the end of the bridge, where it meets up with the freeway. Those connectors offer the concrete enough space to move and prevent concrete cracks.
Expansion joints also come in different sizes and shapes, from molded rubber to clay bricks. Other forms of construction, such as air ducts and railways, have specialized breather joints intended to deal with its distinctive thermal stresses. In short, they fill the gaps between the bridge and function as a flexible filler.
Proper piping alignment is high on the list of priorities when installing expansion joints. An offset installation puts the joints in a difficult situation and may create risks for both operators and products. Expansion joints are not made to compensate for inaccuracies in piping installation and must not be utilized to fix them.
Likewise, the vibration must be lessened, and joints must be positioned as close as possible to fixed anchors or control rods utilized in un-anchored piping systems. Enough pipe support is essential as the expansion joint must not carry the weight of equipment to operate properly.
Expansion joints must not be installed in areas where inspection is not highly possible. Operators must also check for any damage to the unit, install external hardware and ensure it is properly torqued to guarantee leak-free operation.
Expansion joints allow volume change movement of a concrete member or structure. Those are typically designed by installing pre-molded or pre-formed resilient or elastic material of at least ¼ inches to ½ inches thickness as wide as the concrete is thick before the concrete is positioned.
These expansion joints must never be less than ¼ inches wide. Note that pre-molded expansion joints for installation in commercial, residential, or industrial labs may be of sponger rubber, fiber, plastic, or cork composition. Those materials should be extremely resilient and non-extruding in hot weather or brittle in cold weather.
Thinner expansion joints (1/4 inches, 3/8 inches, or ½ inches) spaced at frequent intervals provide better control than thicker expansion joints spaced at greater intervals.
Yes. Expansion joints should be sealed and waterproof regularly to safeguard them against debris, dirt, and water. Such elements can harm the overall structural integrity of the concrete over time. Further, water can result in interior leaks and molds that are expensive to fix. Preventive joint sealing eliminates such risks and restores the concrete for many years to come.
How often concrete expansion joints must be sealed and waterproofed depends on different factors. What is the weather feels like in the area? Is the concrete exposed to heavy traffic? What kind of concrete structure is it, and how old is the concrete.
The joint sealing and waterproofing process varies by structure, but it involves using a product over the expansion joint to make a watertight seal.
After a while, the expansion joint can dry out and not absorb the stress as it once did. That is when cracks show in the concrete slabs. When that happens, it is time to repair and replace the expansion joints. Here are the simple instructions you can follow to repair it:
- Remove any debris and dirt from the area.
- You can use a scraping device or tool, like a 5-in-1, to scrape out your old concrete expansion joint filter.
- Vacuum out the concrete expansion joints.
- Then, use a caulk gun with your filler of choice and then refill the joints again.
- Scape the top and sides of the expansion joints, and you are on your knees for most of it.
- After you are done with the whole scraping process, make sure you follow the curing guidelines of the manufacturer before you allow traffic back on it again.
Correct waterproofing at expansion joints is essential to the longstanding success of the waterproofing application. The continuous movement of such joints could result in openings that enable moisture infiltration if the detail isn’t properly done.
The flashing material used at expansion joints must be reinforced even when the waterproofing structure is an un-reinforced Liquid Applied Membrane system.
If you are waterproofing on vertical applications, you can apply approved sealant in the opening with an approved backer rod to control the sealant’s depth. Use the waterproofing manufacturer’s accepted reinforced flashing material to open and up the vertical substrate.
Remember that the flashing material must be completely adhered to both the horizontal and vertical substrates and must extend a minimum of four inches up the vertical surface.